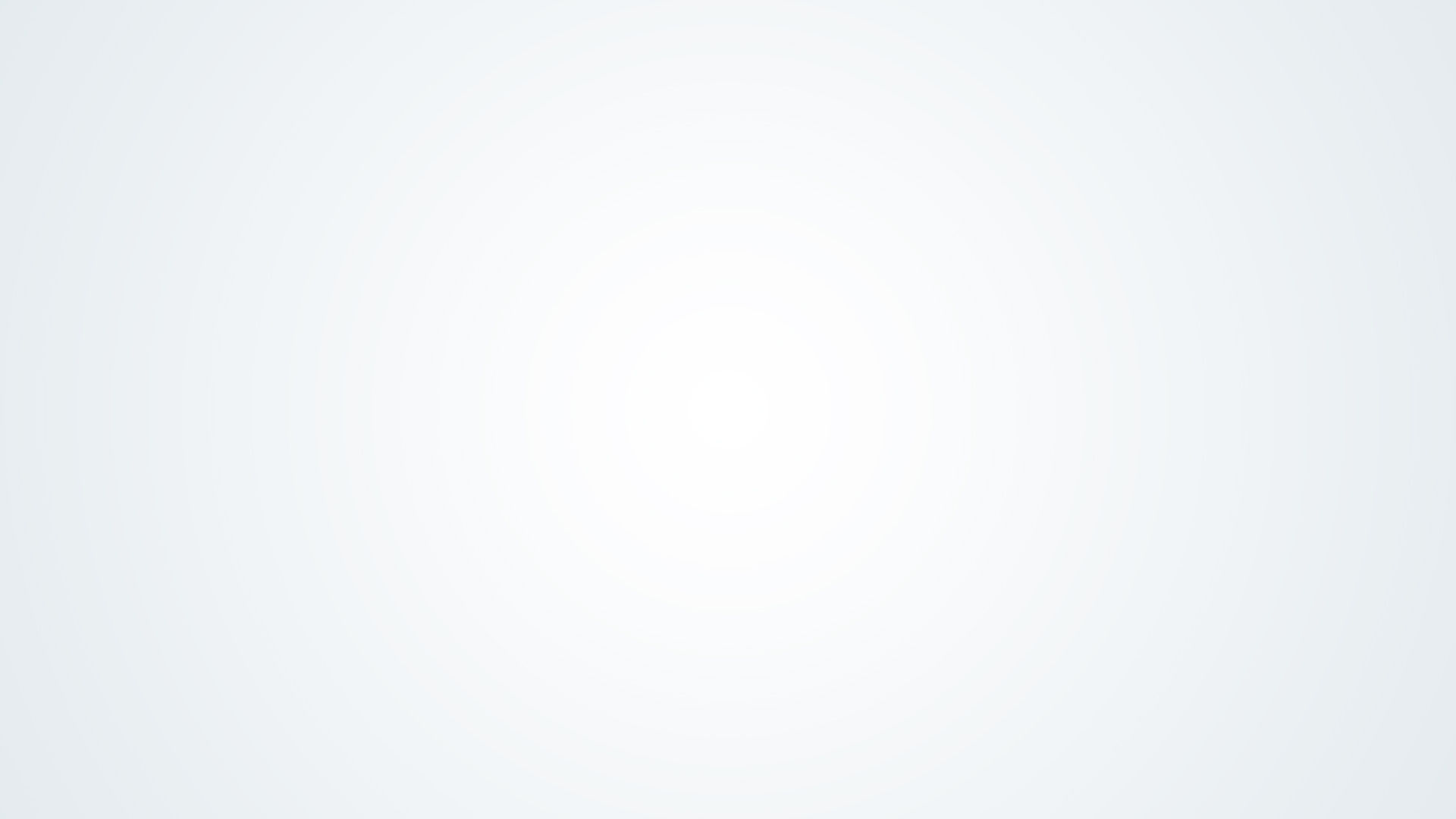
3 steps to making a creme-brulee torch powered engine...




Problem
The Introduction to Machine Design and Prototyping requires only one project and that is to make a sterling engine from all in-house machined pieces of brass, steel, and aluminum. A few drawings are provided but the rest of the specs are open-ended. We just have to make it run, and fast.



Solution
Individuals get busy machining the provided parts learning each piece of equipment in the machine shop - form the mill to the lathe, to the bandsaw and the Prototrack. As pieces begin to "fit" together in the mind, the remaining parts are designed adhering to strict tolerances sometimes are low as one ten-thousandeth of an inch in the case of the piston. Many post machining operations like deburring and lapping are used to make everything fit just right.
Implementation
All the pieces are assembled in Solidworks for a sanity check before attempting to assembly the shiny components with a few fasteners. The End has a empty air reservoir that is heated, causing the air to expand and push a piston that turns a crank and creates momentum in a flywheel. This flywheel in turn forces the piston back while the air cool through the heat sink and prepares to undergo the cycle again. This project fit in well with the Thermodynamics class we took and helped solidify many concepts, not to mention open my eyes to the necessity to worship detail, as it can prove the difference in the end. My engine ran at 1200 RPM.